Stainless Steel Wire For Spokes Supplier
Size: Diameter 0.2mm-5.5mm, 5.5mm-12mm
Standard: GB1220, ASTM A 484/484M, EN 10060/ DIN 1013 ASTM A276, EN 10278, DIN 671
Main Grade: 201, 304, 316, 316L, 310s, 409, 430
Finish: Black, NO.1, mill finish, cold draw
product description of Stainless Steel Wire For Spokes
Stainless Steel Wire for Spokes stands at the forefront of critical components that significantly influence the performance and reliability of spoke-style bikes and motorcycles. Notably, the challenges commonly encountered during usage, such as rust and breakage, pose detrimental effects on both the aesthetics and the fundamental aspects of riding comfort and safety.
The choice of material for spokes plays a pivotal role in determining their overall performance. Over recent decades, there has been a gradual transition from traditional carbon steel to the use of stainless steel for spokes. This shift is attributed to the clear advantages that stainless steel products offer in various aspects of environmental sustainability, mechanical robustness, corrosion resistance, and the visual appeal inherent in the manufacturing process.
Presently, a multitude of manufacturers, both domestic and international, have ventured into producing stainless steel tailored explicitly for spokes. These variants include widely recognized stainless steel grades such as SUS304, lCrl8Ni9Ti, lCrl8Ni9Mo, 12Crl8Ni9, 06Crl8Mn3Ni8N, among others. However, the pursuit of stainless steel materials that promise superior performance characteristics remains a focal point of ongoing research and innovation within the industry.
The inherent strengths of stainless steel wire for spokes transcend mere structural integrity. Its resilience against corrosion, enhanced mechanical strength, and refined aesthetics not only extend the longevity of spokes but also elevate the riding experience. This innovation marks a shift towards sustainable materials, ensuring a durable and visually pleasing choice for spokes in diverse biking and motorcycle applications.
As the industry continuously seeks advancements in spoke materials, the Stainless Steel Wire for Spokes emerges as a testament to ongoing progress, promising enhanced performance, durability, and aesthetics, ushering in a new era of biking excellence.
specification of Stainless Steel Wire For Spokes
Production Range of stainless steel spokes
Size: Diameter 0.2mm-5.5mm, 5.5mm-12mm
Standard: GB1220, ASTM A 484/484M, EN 10060/ DIN 1013 ASTM A276, EN 10278, DIN 671
Main Grade: 201, 304, 316, 316L, 310s, 409, 430
Finish: Black, NO.1, mill finish, cold draw
mechanical property of stainless steel spokes
201 | Y.S./Mpa ≥ | T.S./Mpa ≥ | E.L./% ≥ | HB ≤ | HRB ≤ | HBW ≤ | HV ≤ |
ASTM | 260 | 515 | 40 | – | 95 | 217 | – |
JIS | 275 | 520 | 40 | 241 | 100 | – | 253 |
GB | 205 | 515 | 30 | - | 99 | – | - |
202 | Y.S./Mpa ≥ | T.S./Mpa ≥ | E.L./% ≥ | HB ≤ | HRB ≤ | HBW ≤ | HV ≤ |
ASTM | 260 | 620 | 40 | – | – | 241 | – |
JIS | 275 | 520 | 40 | – | 95 | 207 | 218 |
GB | – | – | – | – | – | – | – |
304 | Y.S./Mpa ≥ | T.S./Mpa ≥ | E.L./% ≥ | HB ≤ | HRB ≤ | HBW ≤ | HV ≤ |
ASTM | 205 | 515 | 40 | – | 92 | 201 | – |
JIS | 205 | 520 | 40 | 187 | 90 | – | 200 |
GB | 205 | 515 | 40 | – | 92 | 201 | 210 |
316L | Y.S./Mpa ≥ | T.S./Mpa ≥ | E.L./% ≥ | HB ≤ | HRB ≤ | HBW ≤ | HV ≤ |
ASTM | 170 | 485 | 40 | – | 95 | 217 | – |
JIS | 175 | 480 | 40 | 187 | 90 | 200 | |
GB | 170 | 485 | 40 | – | 95 | 217 | 220 |
409 | Y.S./Mpa ≥ | T.S./Mpa ≥ | E.L./% ≥ | HB ≤ | HRB ≤ | HBW ≤ | HV ≤ |
ASTM | – | – | – | – | – | – | – |
JIS | 175 | 360 | 22 | 162 | 80 | – | 175 |
GB | – | – | – | – | – | – | – |
310s | Y.S./Mpa ≥ | T.S./Mpa ≥ | E.L./% ≥ | HB ≤ | HRB ≤ | HBW ≤ | HV ≤ |
ASTM | 205 | 515 | 40 | – | 95 | 217 | – |
JIS | 205 | 520 | 40 | 187 | 90 | – | 200 |
GB | 205 | 515 | 40 | – | 95 | 217 | 220 |
410S | Y.S./Mpa ≥ | T.S./Mpa ≥ | E.L./% ≥ | HB ≤ | HRB ≤ | HBW ≤ | HV ≤ |
ASTM | 205 | 415 | 22 | – | 89 | 183 | – |
JIS | 205 | 410 | 20 | – | 88 | 183 | 200 |
GB | 205 | 415 | 20 | – | 89 | 183 | 200 |
features of Stainless Steel Wire For Spokes
The term “Innocent Bright Surface” encapsulates the pristine and untainted appearance of the stainless steel wire. This surface attribute is achieved through a meticulous manufacturing process that prioritizes the elimination of impurities, contaminants, and surface irregularities.
The brightness of the surface is a result of multiple manufacturing stages, including precision cleaning, polishing, and surface treatment. These processes aim to remove any residues, scale, or discoloration, ensuring a visually flawless surface.
At a microscopic level, the surface of the stainless steel wire exhibits a smooth and reflective finish. The absence of surface imperfections or irregularities contributes to its innocent and unblemished appearance. This characteristic is vital not only for aesthetics but also for functional aspects, as a smooth surface minimizes areas prone to corrosion or stress concentrations.
The innocent bright surface reflects light uniformly, enhancing its visual appeal and contributing to the overall attractiveness of the wire. This immaculate surface finish serves as an indicator of the wire’s quality, indicating the meticulous attention to detail and quality control during the manufacturing process.
Furthermore, this surface characteristic is crucial for applications where cleanliness and visual appeal are paramount, such as in spokes for bicycles and motorcycles. The innocent bright surface not only elevates the aesthetics but also serves as a protective barrier against potential corrosion or environmental degradation, ensuring the wire’s durability and longevity in outdoor settings.
In summary, the innocent bright surface of Stainless Steel Wire for Spokes is the result of a comprehensive manufacturing process that prioritizes cleanliness, smoothness, and uniform reflectivity. This immaculate surface not only enhances the wire’s visual allure but also serves as a testament to its quality and resilience in demanding environments.
Stable mechanical properties are a result of the wire’s inherent composition and the precision of the manufacturing process. Stainless steel wire for spokes is carefully engineered to maintain consistent mechanical characteristics, ensuring predictability and reliability in its behavior under different stress conditions.
At its core, the stability of mechanical properties in this wire denotes minimal variations or deviations in crucial aspects like tensile strength, yield strength, elongation, and resilience over time. This uniformity is achieved through stringent quality control measures and adherence to specific alloy compositions and processing techniques.
The wire’s mechanical properties are directly influenced by its microstructure, which is meticulously controlled during manufacturing. The crystalline structure and arrangement of atoms within the stainless steel wire play a pivotal role in determining its mechanical behavior. Through controlled annealing and processing methods, the wire attains a uniform microstructure, ensuring consistent mechanical attributes throughout its length and cross-section.
Stability in mechanical properties is vital for spokes used in bicycles and motorcycles, as it ensures predictable behavior and performance under varying loads, stresses, and environmental conditions. It guarantees that the wire will maintain its structural integrity and perform as intended, even in demanding applications.
Moreover, this stability also enables engineers, designers, and manufacturers to accurately predict the wire’s behavior in different scenarios, allowing for precise design considerations and calculations in various bike components, thereby ensuring safety, reliability, and optimal performance.
In summary, the stable mechanical properties of Stainless Steel Wire for Spokes result from precise control of its composition, processing, and microstructural characteristics. This consistency ensures reliability, predictability, and resilience in the wire’s performance, meeting the demanding requirements of spokes in bikes and motorcycles.
Anti-fatigue performance refers to the wire’s ability to withstand cyclic loading, repetitive stress, and deformation without succumbing to structural failure. In spokes for bicycles and motorcycles, where repetitive stress occurs during riding, this attribute is paramount.
The wire’s excellent anti-fatigue performance is an outcome of its inherent material properties and specialized manufacturing processes. Stainless steel, known for its durability and resilience, is meticulously processed to enhance its fatigue resistance. Through controlled alloy compositions, heat treatments, and surface finishes, the wire is engineered to resist fatigue-induced damage.
At a microscopic level, the wire’s microstructure plays a pivotal role. Its fine-grained and homogenous structure helps distribute stress more uniformly, minimizing stress concentrations that could lead to fatigue cracks. This robust microstructure, achieved through precise manufacturing techniques, fortifies the wire against cyclic loading.
Moreover, the wire’s resistance to fatigue is assessed through rigorous testing methods that simulate real-world cycling conditions. These tests include cyclic loading evaluations, bending fatigue tests, and stress endurance assessments to ensure the wire’s ability to withstand repetitive stress cycles without compromising its structural integrity.
The exceptional anti-fatigue performance of Stainless Steel Wire for Spokes not only prolongs its service life but also ensures safety and reliability during prolonged usage. It minimizes the risk of failure due to cyclic loading, providing riders with confidence in the durability of their biking components.
Furthermore, in demanding applications where reliability and safety are paramount, such as bicycle and motorcycle spokes, this characteristic sets the stainless steel wire apart by offering extended service life and maintaining performance under repetitive stress conditions.
In essence, the excellent anti-fatigue performance of Stainless Steel Wire for Spokes is a result of its engineered material properties, microstructural integrity, and rigorous testing, ensuring durability and reliability in cyclic loading scenarios, vital for spokes’ functionality in biking and motorcycle applications.
Superior rust resistance in stainless steel wire arises from its inherent composition, primarily chromium content, and the formation of a protective oxide layer on its surface. Chromium, an essential alloying element in stainless steel, reacts with oxygen to form a thin and stable chromium oxide layer, known as the passive layer, on the wire’s surface.
This passive layer acts as a protective barrier, preventing further oxidation and corrosion by blocking the access of corrosive agents like moisture and oxygen to the underlying metal. The stability and integrity of this chromium oxide layer contribute significantly to the wire’s resistance against rust or corrosion.
Furthermore, the presence of additional alloying elements, such as nickel and molybdenum in certain stainless steel grades, enhances the wire’s corrosion resistance. These alloying elements promote the formation and stability of the protective oxide layer, augmenting the wire’s ability to withstand corrosive environments, including exposure to moisture, salts, and contaminants.
The wire’s resistance to rust is rigorously evaluated through industry-standard corrosion tests, simulating real-world conditions where exposure to moisture, humidity, and corrosive elements is common. These tests confirm the wire’s ability to maintain its structural integrity and appearance even after prolonged exposure to corrosive environments.
The superior rust resistance of Stainless Steel Wire for Spokes is crucial for outdoor applications like bicycles and motorcycles, where exposure to varying weather conditions and environmental elements is inevitable. This resistance ensures the wire’s durability, preventing surface degradation, pitting, or structural weakening due to corrosion.
In summary, the superior rust resistance of Stainless Steel Wire for Spokes is a result of its alloy composition, especially chromium content, which forms a protective oxide layer. This protective layer shields the wire from corrosion, ensuring durability and reliability in diverse environmental conditions, making it an ideal choice for outdoor applications in biking and motorcycle components.
application of Stainless Steel Wire For Spokes
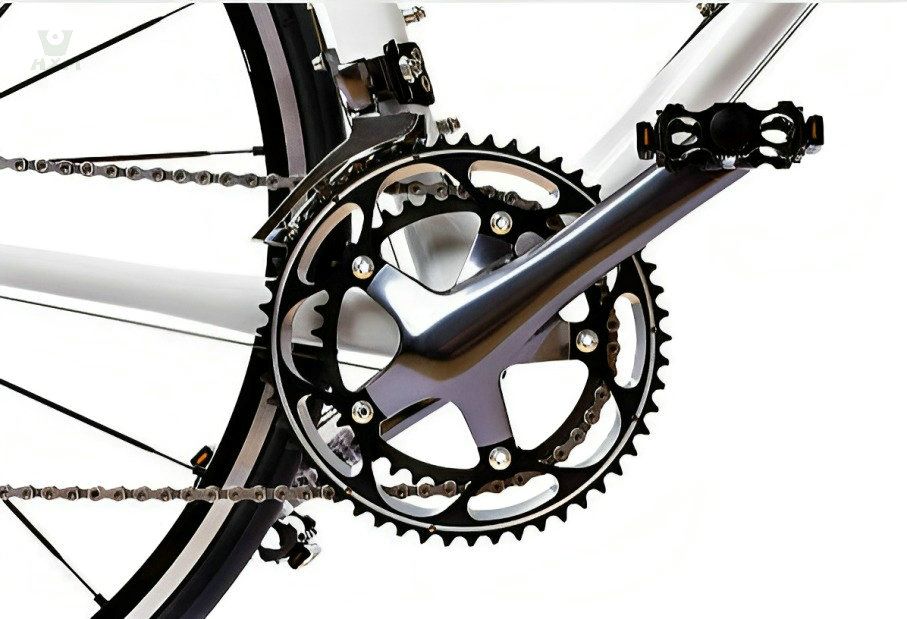
High-End Bicycles
Stainless steel spokes are integral components in wheel assembly, providing structural support and stability. Their strength and quality are vital for the overall robustness of the wheel. For high-performance bicycles, stainless steel spokes offer an optimized strength-to-weight ratio, catering to lightweight design and enhanced performance requirements.
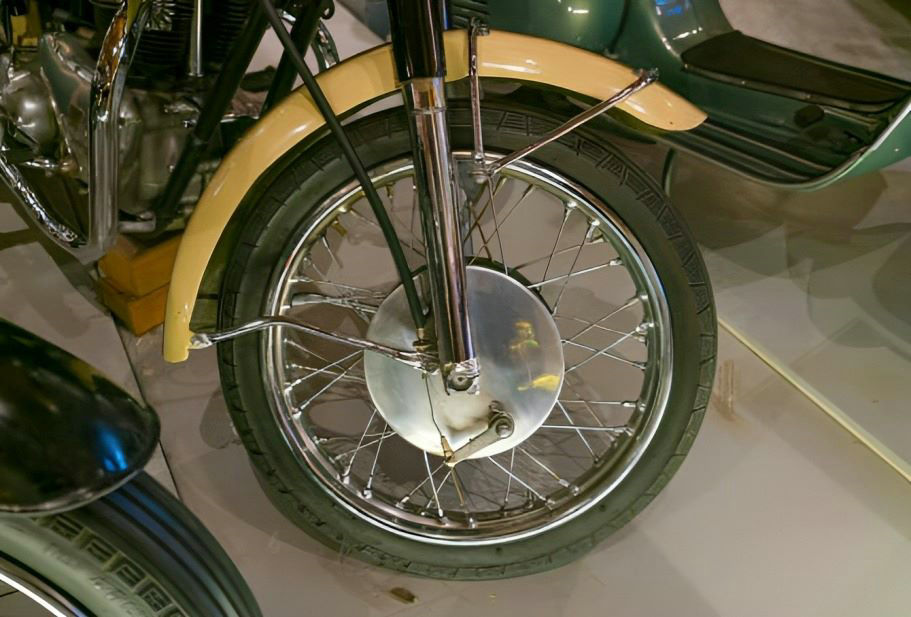
Motorcycles
Stainless steel spokes play a crucial role in maintaining stability and structural integrity in motorcycle wheels. Especially crucial when motorcycles traverse demanding riding conditions and diverse terrains.
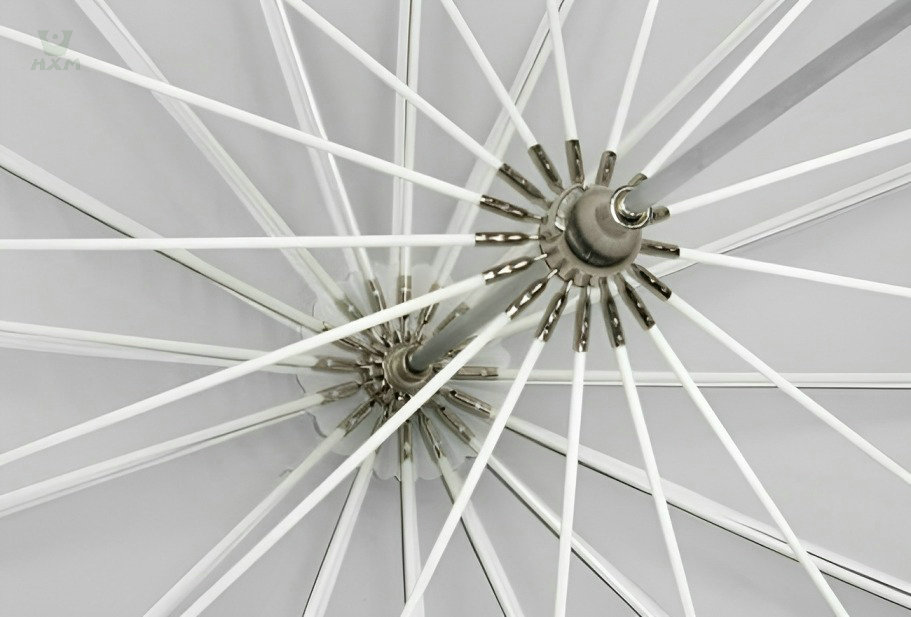
Umbrella Frames
Stainless steel spokes are employed in the construction of umbrella frames, providing structural support and resilience. Their durability and resistance to corrosion make them suitable for enduring exposure to varying weather conditions, ensuring the stability and longevity of umbrella structures.
FAQ
Selecting the optimal material for bike spokes necessitates consideration of various factors, with stainless steel emerging as the preferred choice for numerous compelling reasons.
Stainless Steel for Bike Spokes:
Material Durability: Stainless steel, owing to its inherent durability and resilience, stands out as an ideal choice for bike spokes. The material’s robustness ensures that the spokes endure repeated stress and load-bearing requirements encountered during bike riding.
Corrosion Resistance: Stainless steel’s exceptional resistance to corrosion and rust makes it particularly suitable for outdoor applications. Stainless steel spokes mitigate the risk of corrosion, maintaining their structural integrity even when exposed to varying weather conditions and environmental elements.
Mechanical Strength: The mechanical strength of stainless steel spokes is paramount for withstanding the forces experienced during biking. Stainless steel wires, engineered specifically for spokes, possess high tensile strength and sufficient flexibility, ensuring they endure the rigors of biking without compromising performance.
Manufacturing Precision: Stainless steel wire manufacturers specialize in crafting spokes designed to meet specific strength and durability requirements. Their expertise ensures the production of spokes with consistent quality, adhering to industry standards for performance and reliability.
Weight-to-Strength Ratio: Stainless steel spokes strike a balance between strength and weight, crucial for enhancing bike performance. They offer sufficient strength while keeping the overall weight of the wheel assembly in check, contributing to the bike’s maneuverability and agility.
Longevity: Stainless steel spokes, specifically designed for bike applications, exhibit exceptional longevity. They maintain their structural integrity over extended periods, reducing the need for frequent replacements or maintenance.
In essence, stainless steel emerges as the best material for bike spokes due to its exceptional durability, corrosion resistance, mechanical strength, and expertise in manufacturing by stainless steel wire manufacturers. Its ability to endure the demanding conditions of biking while ensuring longevity and reliability solidifies its position as the optimal choice for bike spoke construction.
Protecting stainless steel spokes from rust involves implementing several measures to maintain their corrosion-resistant properties:
Regular Cleaning: Initiate a maintenance routine by cleaning stainless steel spokes with a mild detergent and water solution. Ensure thorough rinsing and drying to prevent water spots or residue buildup that may lead to localized corrosion.
Avoid Harsh Chemicals: Refrain from using abrasive or acidic cleaners that can compromise the passive layer of the stainless steel spokes, making them susceptible to corrosion. Opt for gentle cleaners approved for stainless steel.
Protective Coatings: Consider applying a protective coating or treatment designed for stainless steel spokes. Some manufacturers offer specialized coatings that enhance the material’s natural resistance to rust and environmental elements, prolonging their lifespan.
Routine Inspections: Periodically inspect the spokes for any signs of damage, scratches, or areas where the protective surface might be compromised. Promptly address any issues to prevent corrosion from spreading.
Proper Storage: Store bikes or wheel assemblies in a dry and sheltered environment when not in use. Avoid prolonged exposure to moisture, which can accelerate the onset of rust on stainless steel spokes.
Utilize Lubricants: Apply a thin layer of specific lubricants or protectants designed for stainless steel spokes. These products act as a barrier against moisture and contaminants, safeguarding the spokes from rust formation.
Professional Consultation: Seek guidance from stainless steel wire manufacturers or suppliers specializing in stainless steel spokes. They may offer recommendations, treatments, or products specifically tailored to protect stainless steel spokes from rust and maintain their longevity.
Implementing these preventive measures in regular maintenance routines ensures the prolonged lifespan and corrosion resistance of stainless steel spokes, safeguarding them against rust and preserving their structural integrity.
Stainless steel spokes typically exhibit weak magnetic properties due to their composition, primarily comprising an alloy of iron, chromium, nickel, and other elements.
Magnetism in Stainless Steel Spokes:
Weak Magnetic Response: Stainless steel spokes commonly demonstrate weak magnetic properties, especially in comparison to ferromagnetic materials like regular carbon steel. The addition of chromium and nickel in stainless steel alloys reduces the overall magnetic permeability.
Austenitic Stainless Steel: Many stainless steel wire manufacturers utilize austenitic stainless steel for spokes, which is non-magnetic or exhibits very low magnetism. This type of stainless steel, containing nickel and high chromium content, tends to be non-magnetic in its annealed state.
Effect of Processing: The magnetic properties of stainless steel spokes can vary based on their specific alloy composition, heat treatment, and manufacturing processes. Cold-working or deformation during the spoke-making process may induce slight magnetism in some cases.
Detection Using Magnets: While stainless steel spokes typically display weak magnetic characteristics, they might attract a magnet to some extent. However, this magnetism is notably weaker than that observed in ferromagnetic materials, making it less prominent and easily distinguishable.
In summary, stainless steel spokes often possess weak magnetic properties due to their composition, but the extent of magnetism can vary based on the specific alloy used, manufacturing processes, and treatment. Stainless steel wire for spokes, particularly of the austenitic type, is generally recognized for its minimal magnetic response.
Stainless steel spokes are generally comparable in strength to traditional steel spokes, depending on the specific grade, diameter, and manufacturing processes used.
Strength of Stainless Steel Spokes Compared to Steel:
Material Characteristics: Stainless steel wire for spokes and traditional steel spokes possess differing material properties based on their composition. Stainless steel is an alloy containing chromium, nickel, and other elements, offering excellent corrosion resistance. Traditional steel spokes are usually made from carbon steel, known for its strength but lacking in corrosion resistance.
Strength-to-Weight Ratio: Stainless steel spokes and steel spokes often have a similar strength-to-weight ratio. While stainless steel may have slightly lower tensile strength compared to some high-grade carbon steels, the difference is often negligible for practical purposes in spoke applications.
Manufacturing Processes: Stainless steel wire manufacturers employ specific processes to create spokes tailored for strength and durability. Similar manufacturing techniques are used for traditional steel spokes. The strength of spokes can be influenced by factors such as heat treatment, drawing processes, and alloy composition adjustments.
Corrosion Resistance vs. Strength: Stainless steel spokes excel in corrosion resistance, making them preferable in environments prone to moisture and rust. While traditional steel spokes may exhibit marginally higher tensile strength, they lack the corrosion resistance offered by stainless steel.
Application Suitability: Both stainless steel and traditional steel spokes meet the necessary strength requirements for their intended applications in bike wheels. The choice between the two often depends on preferences related to corrosion resistance, weight considerations, and environmental factors.
In essence, while there might be minor differences in specific grades or alloys, both stainless steel and traditional steel spokes generally offer comparable strength suitable for bike wheel applications. The decision between the two often involves considering factors beyond pure strength, such as corrosion resistance and overall durability in different environmental conditions.
Get In touch
Ready to Elevate Your Projects? Dive into our Stainless Steel Collection and Submit Your Specifications Today!
Phone/WhatsApp/WeChat:
+86 13052085117
Email: [email protected]
Address: RM557, NO.1388 Jiangyue Road, Shanghai China