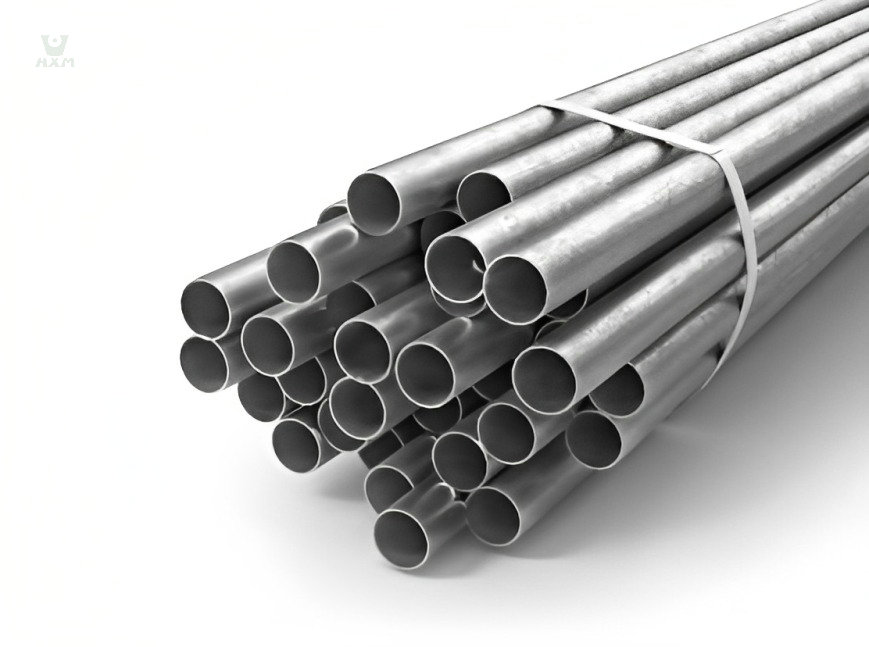
347 Stainless Steel Welded Tube Suppliers
Specification: Alloy 347, ASTM A213 TP 347, UNS S34700, ASTM A312 TP347 steel pipe
Size Range: From 4mm4mm to 800mm800mm
Wall Thickness Range: From 1mm to 150mm (SCH10-XXS)
Length Options: 4000mm, 5800mm, 6000mm, 12000mm, or as required.
Finish: 2B, BA,4K,8K, NO.1,2D,3#, HL
Type: Round, square, rectangular, hexagonal, flat, angle
Technique: Cold rolled, hot rolled
Payment method: T/T, LC
Price: Inquiry Now
347 Stainless Steel Welded Tube Data Sheet
Chemical Components Of 347 Stainless Steel Welded Tube
Element | ASTM A240 | JIS G4304 | EN 10088-2 | GB/T 4237 |
Chromium (Cr) | 17.0-19.0 | 17.0-19.0 | 17.0-19.0 | 17.0-19.0 |
Nickel (Ni) | 9.0-13.0 | 9.0-13.0 | 9.0-13.0 | 9.0-13.0 |
Carbon (C) | ≤ 0.08 | ≤ 0.08 | ≤ 0.08 | ≤ 0.08 |
Manganese (Mn) | ≤ 2.00 | ≤ 2.00 | ≤ 2.00 | ≤ 2.00 |
Phosphorus (P) | ≤ 0.045 | ≤ 0.045 | ≤ 0.045 | ≤ 0.045 |
Sulfur (S) | ≤ 0.03 | ≤ 0.03 | ≤ 0.03 | ≤ 0.03 |
Silicon (Si) | ≤ 1.00 | ≤ 1.00 | ≤ 1.00 | ≤ 1.00 |
Columbium & Tantalum (Cb+Ta) [^1^][1] [^2^][3] [^3^][4] | ≥10(C+N)-1, max:1.00 | ≥10(C+N)-1, max:1.00 | ≥10(C+N)-1, max:1.00 | ≥10(C+N)-1, max:1.00 |
Physical Properties Of 347 Stainless Steel Welded Tube
Property | Value |
Density | 0.288 lb./in³ / (7.96 g/cm³) 1 |
Modulus of Elasticity (E) | 28.0 x 10³ ksi / (193 x 10³MPa) 1 |
Coefficient of Expansion | 9.2 x 10 -6 microinches/in.-°F (70-600°F) / (16.6 μm/m-°C) (20-300°C) 1 |
Electrical Resistivity | 28.4 μ ohm.in / (72 μ ohm.cm) 1 |
Thermal Conductivity | 9.5 Btu-in./ft.²hr.-°F / (16.3 W/m-K) 1 |
mechanical Properties Of 347 Stainless Steel Welded Tube
Property | Value |
Tensile Strength | 93 ksi (640 MPa) |
Yield Strength | 37 ksi (250 MPa) |
Elongation in 2″ | 45% |
Hardness | Rockwell 84 HRBW |
Product Description Of 347 Stainless Steel Welded Tube
If you’re in search of a high-quality, durable stainless steel pipe capable of withstanding both high temperatures and corrosive environments, our 347 stainless steel welded pipe should be on your radar. Our 347 stainless steel welded pipe is crafted from stable austenitic stainless steel, excelling in its resistance to intergranular corrosion within the carbide-chromium precipitation temperature range of 800 – 1500°F (427 – 816°C). Moreover, it boasts impressive oxidation resistance, exceptional creep strength up to 816°C (1500°F), and remarkable low-temperature toughness.
What sets our 347 stainless steel welded pipe apart is not only its exceptional formability and welding quality but also its seamless integration into standard workshop procedures. It finds versatile applications across various industries, including chemical processing, food processing, petroleum refining, and waste heat recovery.
Compared to 304 stainless steel, our 347 stainless steel welded pipe stands out with higher creep stress and fracture performance. Its adaptability extends to a wide array of sizes, shapes, and surface treatments to cater to your specific needs.
Contact us today to receive a quote for our 347 stainless steel welded pipe and discover the myriad benefits of this versatile and reliable product. Our solution is a unique combination of durability, performance, and customization that sets it apart from the rest.
Features Of 347 Stainless Steel Welded Tube
347 stainless steel welded tube has excellent resistance to intergranular corrosion after exposure to temperatures in the chromium carbide precipitation range of 800 – 1500°F (427 – 816°C). It also has good oxidation resistance and creep strength to 1500°F (816°C), as well as good low temperature toughness.
Our 347 stainless steel welded tube has excellent forming and welding qualities and can be easily fabricated by standard shop practices .
Intergranular corrosion, a phenomenon that occurs along the grain boundaries of a material, can significantly compromise the structural integrity and longevity of stainless steel. However, 347 stainless steel welded tubes exhibit impressive resistance to this type of corrosion due to their unique composition and processing.
The key factor contributing to the intergranular corrosion resistance of 347 stainless steel is its niobium content. Niobium, also known as columbium, forms stable carbides with carbon, preventing the chromium from precipitating out of the alloy as chromium carbides along the grain boundaries. This phenomenon, known as sensitization, is a primary cause of intergranular corrosion.
By inhibiting sensitization, niobium ensures that the grain boundaries remain free from chromium-depleted zones, maintaining the overall corrosion resistance of the material. This property is particularly valuable in applications where exposure to high temperatures can trigger sensitization and subsequent intergranular corrosion.
In 347 stainless steel welded tubes, the intergranular corrosion resistance is further enhanced by the controlled addition of titanium. The formation of titanium carbides at elevated temperatures helps to bind any available carbon, leaving chromium in the alloy to form a protective oxide layer, which prevents corrosive agents from attacking the grain boundaries.
Oxidation, a chemical reaction between a material and oxygen, can lead to the degradation of metals, particularly at elevated temperatures. However, 347 stainless steel welded tubes are well-known for their remarkable oxidation resistance, making them an ideal choice for applications in high-temperature environments.
The impressive oxidation resistance of 347 stainless steel is primarily attributed to its chromium content. Chromium forms a thin, adherent oxide layer on the surface of the material when exposed to oxygen. This protective oxide layer acts as a barrier, preventing further reaction between the metal and oxygen, effectively shielding the underlying material from oxidation.
Additionally, the inclusion of niobium in the composition of 347 stainless steel further enhances its oxidation resistance. Niobium stabilizes the material’s microstructure at high temperatures, reducing the formation of chromium carbides that could otherwise lead to sensitization and subsequent degradation.
In industries and applications where extreme temperatures are a constant factor, the performance of materials is put to the test. This is where the high temperature performance of 347 stainless steel welded tubes shines. These tubes are specifically designed to maintain their structural integrity and mechanical properties even when subjected to elevated temperatures.
The key to the high temperature performance of 347 stainless steel lies in its composition. The addition of niobium, also known as columbium, plays a crucial role. Niobium forms stable carbides that prevent the precipitation of harmful chromium carbides at elevated temperatures, a phenomenon known as sensitization. This ensures that the material remains resistant to intergranular corrosion and maintains its toughness and strength, even when exposed to high heat.
The 347 stainless steel welded tubes can operate at temperatures ranging from 800 to 1500°F (427 to 816°C), making them well-suited for applications in industries like petrochemical, aerospace, and power generation. Their ability to withstand these temperatures without compromising their properties makes them a reliable choice for components that operate under extreme conditions.
Furthermore, the high temperature performance of these tubes is not limited to their mechanical properties alone. They also exhibit excellent oxidation resistance, which means that they can maintain their surface quality and appearance even at elevated temperatures. This attribute is particularly valuable for applications where aesthetics and functionality go hand in hand.
In demanding industrial applications, where materials are exposed to prolonged elevated temperatures, creep becomes a significant consideration. Creep is the gradual deformation that occurs in materials over time when subjected to constant stress at high temperatures. The creep strength of 347 stainless steel welded tubes makes them a preferred choice for such environments.
The addition of niobium (columbium) in the composition of 347 stainless steel plays a crucial role in enhancing its creep strength. Niobium forms stable carbides that resist the formation of harmful precipitates, ensuring the material’s resistance to sensitization even during long-term exposure to elevated temperatures.
The 347 stainless steel welded tubes exhibit excellent creep resistance within the temperature range of 800 to 1500°F (427 to 816°C). This property is particularly vital in applications like petrochemical processing, thermal power generation, and aerospace, where components need to withstand constant stress at high temperatures without significant deformation.
The superior creep strength of these tubes is a result of their careful alloy design and manufacturing processes. This aspect sets them apart from standard stainless steels, making them a reliable choice for applications that demand consistent performance over extended periods in challenging conditions.
While high-temperature performance is crucial, the ability of a material to maintain its mechanical properties in low-temperature environments is equally important, especially in industries like cryogenics, aerospace, and chemical processing. The low-temperature toughness of 347 stainless steel welded tubes makes them a reliable choice for such applications.
The composition of 347 stainless steel includes elements like niobium and titanium, which contribute to the alloy’s enhanced low-temperature properties. These elements aid in stabilizing the material’s microstructure, preventing the formation of harmful phases that can lead to embrittlement.
The low-temperature toughness of these tubes is evident in their ability to resist brittle fracture even when subjected to sub-zero temperatures. This property ensures that the tubes maintain their structural integrity and mechanical strength in extreme cold conditions, safeguarding the performance of critical components and systems.
The improved low-temperature toughness of 347 stainless steel welded tubes makes them well-suited for applications in Arctic environments, cryogenic storage, and any scenario where exposure to low temperatures is a concern. Their ability to withstand cold-induced stresses without compromising on performance highlights their reliability and versatility.
Application Of 347 Stainless Steel Welded Tube
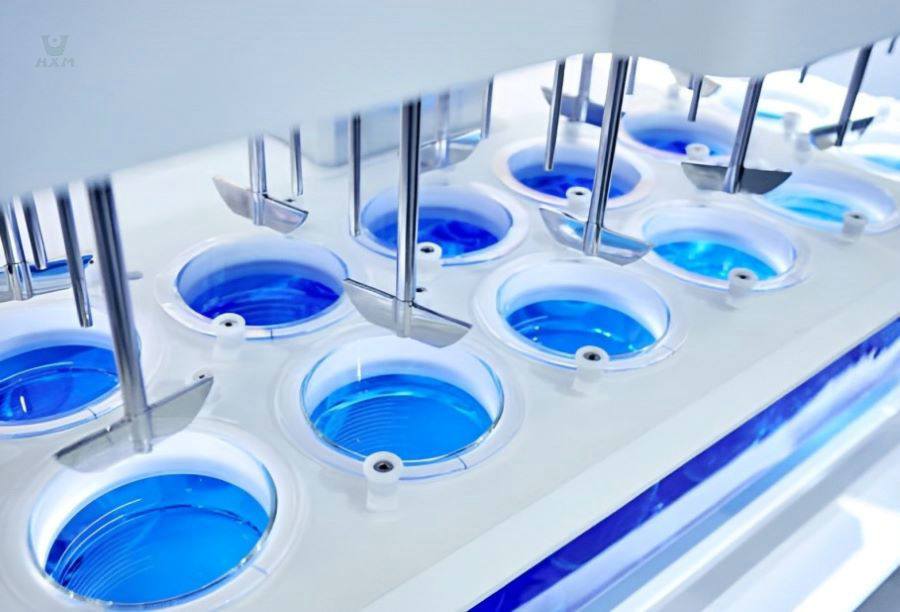
chemical processing applications
347 stainless steel welded tubes find extensive use in a wide range of chemical processing applications due to their exceptional qualities. These tubes are especially suited for tasks like distillation columns, where they handle high-temperature and corrosive environments. They're also vital in chemical reactors, effectively resisting corrosive substances. Additionally, their presence in heat exchangers ensures efficient heat transfer while maintaining their corrosion resistance. Huaxiao stainless steel tube suppliers offer reliable access to these tubes, meeting the demanding requirements of the chemical processing industry.
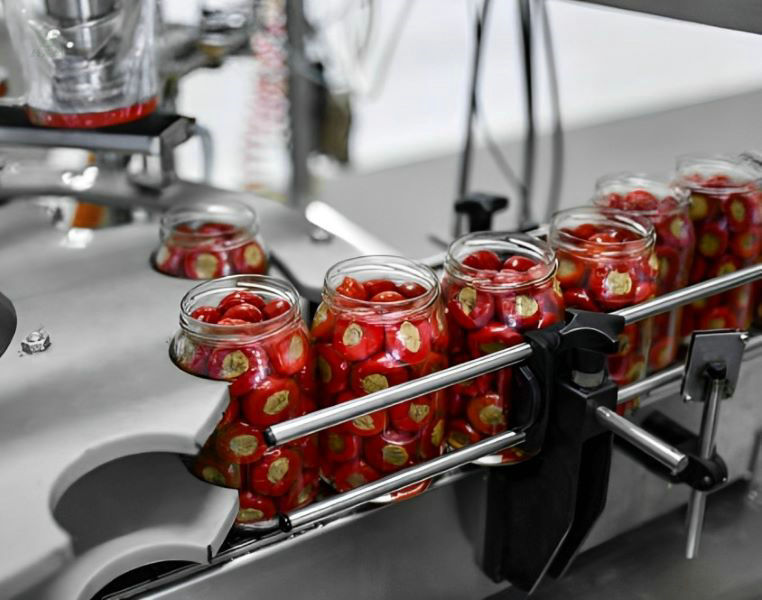
food processing sector
347 stainless steel welded tubes play a crucial role in the food processing sector, demonstrating exceptional suitability for equipment like ovens, fryers, and sterilizers. Due to their corrosion resistance and high-temperature capabilities, these tubes ensure food safety and product integrity. Their presence in such equipment guarantees reliable and efficient operations in food processing facilities. When sourcing these tubes, manufacturers can rely on like Huaxiao stainless steel tube suppliers for quality and reliability.
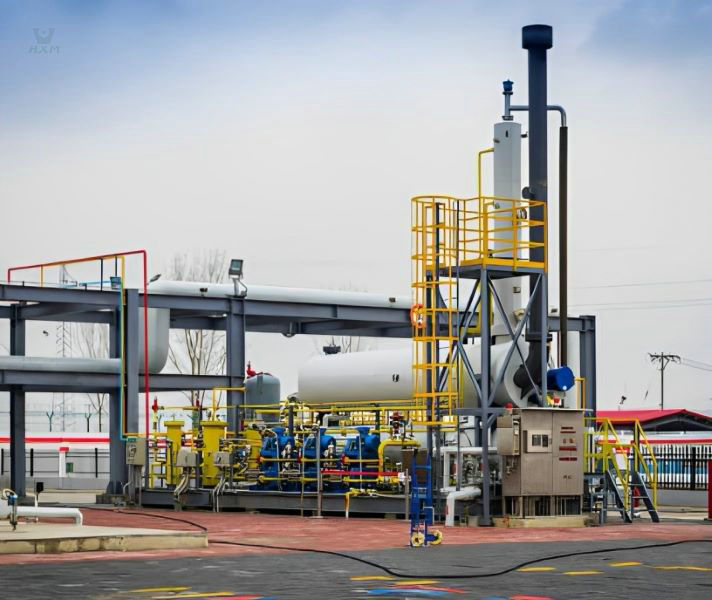
petroleum refining sector
In the realm of petroleum refining, 347 stainless steel welded tubes play a vital role in various equipment, including heat exchangers, piping systems, and pressure vessels. These tubes are specifically chosen for their exceptional resistance to high-temperature and corrosive environments encountered in refining processes. Their presence ensures the integrity and efficiency of petroleum refining operations. When seeking these tubes, Huaxiao stainless steel tube suppliers can provide the necessary quality and expertise for such critical applications.
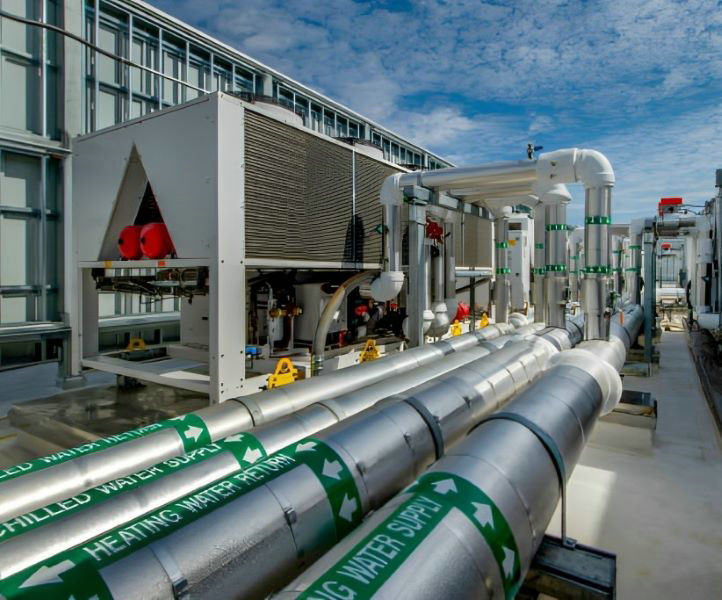
Waste heat recovery systems
Waste heat recovery systems play a crucial role in improving energy efficiency by harnessing the untapped thermal energy from exhaust gases and high-temperature processes. 347 stainless steel welded tubes are employed in these systems due to their exceptional heat resistance and corrosion resilience. These tubes facilitate the transfer of heat from exhaust gases to a heat exchanger, where the captured energy can be used for various applications, such as heating water or generating power. By utilizing 347 stainless steel tubes in waste heat recovery, industries can reduce energy wastage, lower operational costs, and contribute to sustainable practices.
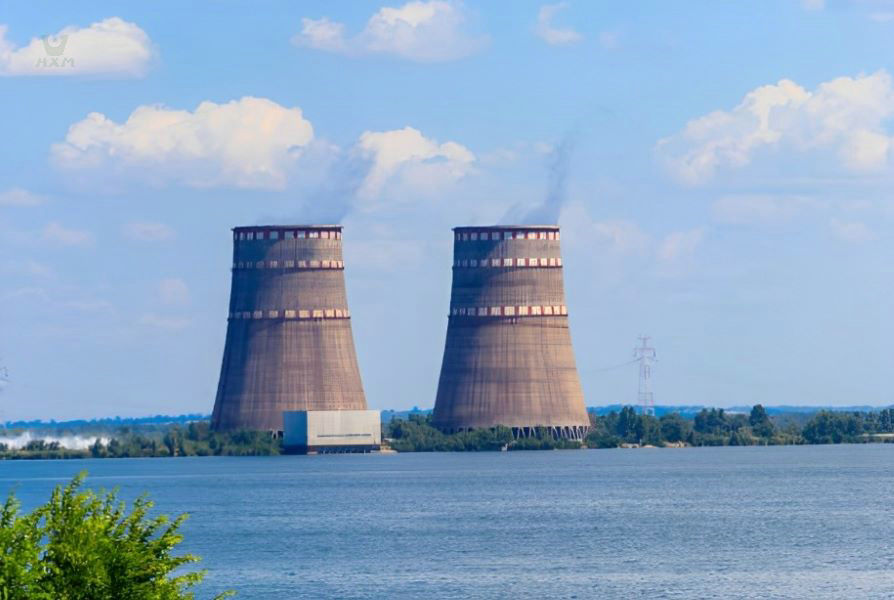
power generation systems
347 stainless steel welded tubes are essential components in power generation systems. These tubes are used in various power plants, including thermal, nuclear, and renewable energy facilities. They play a crucial role in heat exchange processes, where they transfer thermal energy between different mediums, such as water and steam. This efficient heat transfer helps drive turbines and generators, ultimately producing electricity. The high temperature and corrosion resistance of 347 stainless steel make it a reliable choice for withstanding the demanding conditions of power generation environments.
FAQ
Welding stainless steel tubes requires careful attention to detail. It doesn’t dissipate heat as well as mild steel or aluminum, and it can lose some of its corrosion resistance if too much heat is put into it. Best practices can contribute to maintaining its corrosion resistance. Here are some tips for welding stainless steel tubes:
Select a low-carbon filler metal when welding stainless steel: In stainless steel welding, filler metal selection is crucial to controlling carbon levels. The filler metal used for stainless steel tube and pipe welding should enhance the weld properties and meet the application requirements. Look for filler metals with an “L” designation, such as ER308L, because these provide a lower maximum carbon content, which helps retain corrosion resistance in low-carbon stainless alloys. Welding a low-carbon base material with a standard filler metal can increase the carbon content of the weld joint and thereby increase the risk of corrosion.
Pay attention to weld preparation and proper fit-up: Because stainless steel is so sensitive to heat input, joint preparation and proper fit-up play key roles in controlling the heat to maintain the material’s properties. With gaps or uneven fit-up between the parts, the torch must stay in one spot longer, and more filler metal is needed to fill those gaps. This results in heat buildup in the affected area, which can overheat the part. Poor fit-up also can make it harder to bridge gaps and get the necessary weld penetration.
Use a low heat input: Because stainless steel doesn’t dissipate heat as well as mild steel or aluminum do, it’s important to use a low heat input when welding it. This helps prevent overheating and loss of corrosion resistance.
Use a shielding gas: Shielding gas is used to protect the weld from atmospheric contamination. Argon is commonly used as a shielding gas for welding stainless steel tubes.
Use proper welding techniques: There are several welding techniques that can be used for welding stainless steel tubes, including gas tungsten arc welding (GTAW), gas metal arc welding (GMAW), and plasma arc welding (PAW). GTAW is the traditional method for welding stainless steel tube and pipe, but using wire welding processes is becoming more common with stainless steel tube and pipe.
The main difference between 347 and 321 stainless steel lies in their titanium content. Both are stabilized austenitic stainless steels, but 347 contains niobium (columbium) and a slightly higher level of chromium, while 321 has titanium as its stabilizing element. This difference in stabilizing elements affects their performance in high-temperature applications. 347 stainless steel is better suited for elevated temperature service due to the presence of niobium, which offers improved resistance to sensitization and intergranular corrosion. On the other hand, 321 stainless steel, with its titanium stabilization, is preferred when excellent resistance to intergranular corrosion is required in lower temperature ranges. Both alloys exhibit good corrosion resistance, weldability, and formability, making them suitable for various applications in industries such as aerospace, chemical processing, and power generation.
Yes, 347 stainless steel is highly suitable for high-temperature applications. It offers excellent heat resistance and stability at elevated temperatures, making it a preferred choice for industries such as aerospace, power generation, and furnace components. The addition of niobium (columbium) to 347 stainless steel helps prevent sensitization and intergranular corrosion, ensuring its performance even in environments with frequent temperature fluctuations. This alloy’s ability to maintain its mechanical properties and corrosion resistance at high temperatures makes it a reliable option for demanding high-temperature applications.
Yes, 347 stainless steel can be welded. It has good weldability and can be easily welded using common welding methods such as TIG (Tungsten Inert Gas) welding, MIG (Metal Inert Gas) welding, and submerged arc welding. However, it’s important to use low carbon versions of the filler material to avoid sensitization and intergranular corrosion. Additionally, post-weld heat treatment may be necessary to ensure the best combination of mechanical properties and corrosion resistance in the welded joints.
No, 347 stainless steel doesn’t typically require special maintenance beyond standard stainless steel care practices. Regular cleaning to remove dirt, grime, and contaminants is recommended. Additionally, avoiding exposure to harsh chemicals and corrosive environments will help maintain its corrosion resistance. Like other stainless steels, routine maintenance will ensure the longevity and performance of 347 stainless steel components.
Yes, 347 stainless steel is generally magnetic. Like many stainless steel alloys, it contains a mixture of both austenite and ferrite phases in its microstructure, which contributes to its magnetic properties. However, the magnetic strength may vary based on factors such as the specific composition and processing of the material.
Yes, custom sizes and lengths of 347 stainless steel welded tubes are often available to meet specific project requirements. You can inquire about these options from Huaxiao stainless steel tube suppliers.